Spis treści
Co to są gazy osłonowe i jaka jest ich rola w spawaniu?
Gazy osłonowe pełnią kluczową rolę w procesie spawania, chroniąc jeziorko spawalnicze oraz elektrodę wolframową przed szkodliwymi czynnikami atmosferycznymi, takimi jak:
- tlen,
- azot,
- wodór.
Obecność tych zanieczyszczeń może prowadzić do poważnych wad w spoinach, w tym utleniania i porowatości, co zdecydowanie wpływa na ich jakość. Dzięki gazom osłonowym możliwe jest zachowanie czystości spoiny oraz zwiększenie jej trwałości. Możemy wyróżnić dwie główne kategorie gazów osłonowych:
- gazy obojętne, wśród których najczęściej stosuje się argon i hel,
- gazy aktywne, takie jak dwutlenek węgla.
Wybór odpowiedniego gazu ma znaczący wpływ na charakterystykę łuku spawalniczego oraz jakość finalnej spoiny. Argon zyskuje popularność w spawaniu stali nierdzewnej i aluminium, dzięki swoim stabilnym właściwościom. Z kolei dwutlenek węgla jest często wybierany do spawania stali czarnej, gdyż sprzyja lepszej penetracji spoiny. Stosowanie gazów osłonowych znacząco obniża ryzyko występowania wad w spawach, co przekłada się na większą solidność całej konstrukcji. Warto pamiętać, że jakość spoiny jest ściśle związana z odpowiednim doborem medium osłonowego, co ma kluczowe znaczenie w zależności od rodzaju materiału oraz wybranej metody spawania.
Jakie gazy są używane w spawaniu stali czarnej?
W procesie spawania stali czarnej stosuje się zazwyczaj dwa główne rodzaje gazów osłonowych:
- dwutlenek węgla (CO2),
- mieszanka argonu z dwutlenkiem węgla (Ar/CO2).
Dwutlenek węgla zyskał popularność dzięki niskim kosztom i wysokiej efektywności, co przyczynia się do uzyskiwania solidnych i trwałych spoin. Choć użycie CO2 wiąże się z większymi rozpryskami podczas spawania, jego atrakcyjność ekonomiczna sprawia, że wiele osób decyduje się na ten gaz. Alternatywą dla czystego CO2 jest mieszanka argonu i dwutlenku węgla, która poprawia stabilność łuku spawalniczego oraz redukuje ilość niepożądanych rozprysków. To z kolei wpływa na podniesienie jakości realizowanych spoin.
Argon, będąc gazem obojętnym, sprzyja lepszej kontroli procesu spawania oraz przyczynia się do estetycznego wyglądu spoin. Wybór odpowiedniego gazu do spawania stali czarnej powinien opierać się na kilku istotnych czynnikach. Z jednej strony, warto uwzględnić specyfikację projektu oraz wymagania dotyczące jakości, a z drugiej – indywidualne preferencje spawacza. Zrozumienie tych aspektów jest kluczowe, jeśli zależy nam na uzyskaniu optymalnych wyników w procesie spawalniczym.
Starannie dobrane gazy osłonowe wpływają nie tylko na jakość wykonanych spoin, ale mają również istotne znaczenie dla bezpieczeństwa pracy oraz trwałości gotowej konstrukcji.
Jakie właściwości mają gazy do spawania?
Gazy stosowane w procesie spawania różnią się pod względem właściwości, co ma ogromny wpływ na jakość wytwarzanych spoin oraz przebieg całej operacji. Na przykład:
- gazy obojętne, takie jak argon czy hel, charakteryzują się wysoką stabilnością i niską reaktywnością,
- dzięki nim można uzyskać czyste spoiny, co znacznie zmniejsza ryzyko utleniania i pojawiania się porowatości,
- argon ma dodatkową zaletę, ponieważ skutecznie kontroluje łuk spawalniczy, co przekłada się na estetykę i trwałość spoin,
- dwa gazy aktywne, takie jak dwutlenek węgla (CO2), wchodzą w reakcję z metalem, co sprzyja lepszemu wtopieniu i penetracji,
- mieszanki gazów, np. argon z CO2, wykorzystują zalety obu rodzajów.
Czystość gazu jest również istotna, ponieważ zanieczyszczenia mogą prowadzić do powstawania wad w spoinach. Dobór odpowiedniego gazu do konkretnego materiału oraz metody spawania ma fundamentalne znaczenie. Właściwie dobrane gazy ochronne nie tylko przyczyniają się do poprawy jakości spoin, ale także wpływają na bezpieczeństwo i zdrowie spawacza.
Dlaczego wybór gazu do spawania jest ważny?
Wybór odpowiedniego gazu do spawania jest niezwykle istotny, ponieważ wpływa bezpośrednio na jakość spoin oraz efektywność całego procesu. Odpowiedni gaz osłonowy jest kluczowy dla:
- stabilności łuku spawalniczego,
- głębokości wtopienia,
- lepszych wyników pracy spawacza.
Na przykład, użycie dwutlenku węgla (CO2) może zwiększyć głębokość penetracji spoiny, ale jednocześnie wiąże się z wyższym ryzykiem rozprysków. Z kolei mieszanka argonu z dwutlenkiem węgla łączy korzystne cechy obu gazów, co sprzyja stabilności łuku i redukcji defektów. Warto również zauważyć, że złe dopasowanie gazu osłonowego może prowadzić do porowatości spoin, co negatywnie wpływa na ich trwałość i bezpieczeństwo całej konstrukcji. Co więcej, jakość spoiny jest silnie uzależniona od czystości zastosowanego gazu; zanieczyszczenia mogą znacząco obniżyć właściwości spawanych materiałów.
Dlatego wybór gazu powinien być przemyślany w kontekście specyfikacji materiałów oraz wymagań projektowych. Ma to kluczowe znaczenie nie tylko dla efektywności pracy spawacza, ale również dla estetyki finalnego produktu. Posiadanie wiedzy o różnych gazach i ich zastosowaniach w spawalnictwie jest nieodłącznym elementem osiągania najlepszych efektów oraz zapewnienia bezpieczeństwa podczas spawania.
Jakie są różnice między gazami aktywnymi a obojętnymi w kontekście spawania?
Gazy aktywne oraz obojętne różnią się w sposób zasadniczy, jeśli chodzi o ich interakcję z metalem podczas procesu spawania. Gazy obojętne, takie jak argon czy hel, nie wchodzą w reakcję z metalem, co pozwala na skuteczne zabezpieczenie spoiny przed utlenieniem oraz zachowanie jej czystości. Jest to istotne, zwłaszcza w przypadku spawania aluminium i stali nierdzewnej. Argon działa stabilizująco na łuk spawalniczy, co znacząco wpływa na estetykę oraz jakość połączenia.
Z drugiej strony, gazy aktywne, takie jak dwutlenek węgla (CO2), reagują chemicznie z metalem, modyfikując jego właściwości. CO2, popularny przy spawaniu stali węglowej, może zwiększyć głębokość wtopienia, jednakże metoda ta pociąga za sobą wyższe ryzyko rozprysków. Wybór odpowiedniego gazu powinien być uzależniony od pożądanych cech spoiny oraz materiału, który spawamy.
Na przykład w przypadku stali czarnej, dwutlenek węgla sprawdza się doskonale, łącząc chemiczne korzyści z niskimi kosztami. Coraz większą popularnością cieszą się także mieszanki gazów, na przykład argon z CO2, które łączą zalety obu rodzajów gazów, poprawiając zarówno jakość spoiny, jak i stabilność procesu. Należy jednak pamiętać, że niewłaściwy wybór gazu może prowadzić do poważnych problemów, takich jak porowatość spoin.
Jakie mieszanki gazów są najczęściej stosowane w spawaniu stali czarnej?
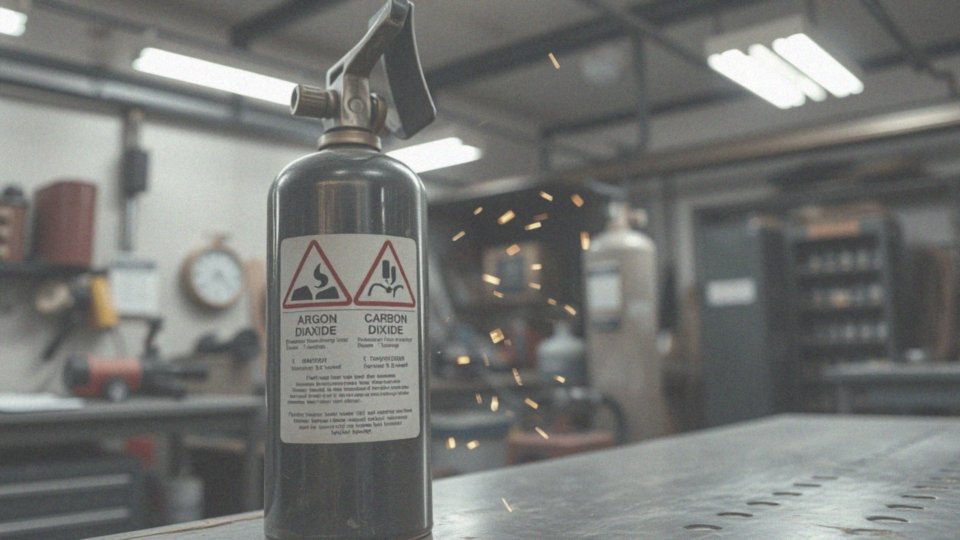
W procesie spawania stali czarnej często wykorzystuje się mieszankę gazów, która łączy argon i dwutlenek węgla (Ar/CO2). Zazwyczaj stosuje się proporcję 82% argonu do 18% CO2. Taka kombinacja wpływa na:
- stabilność łuku spawalniczego,
- zmniejszenie ilości rozprysków,
- podniesienie jakości spoin.
W przypadku grubych materiałów warto rozważyć zwiększenie proporcji dwutlenku węgla, co może poprawić wtopienie, jednak trzeba liczyć się z większą ilością rozprysków. Mieszanka argonu i CO2 łączy korzystne właściwości obu gazów, co przekłada się na lepszą estetykę i wytrzymałość spoin.
Dobór właściwej mieszanki gazowej powinien być uzależniony od kilku istotnych czynników, takich jak:
- grubość spawanego materiału,
- technika spawania,
- wymagania dotyczące jakości połączeń.
Poprawny wybór gazu ma kluczowe znaczenie dla uzyskania trwałych i wysokiej jakości spawów. W kontekście stali czarnej, odpowiedni dobór gazów osłonowych jest fundamentalny. Ma to ogromny wpływ na efektywność spawania oraz na redukcję wad, takich jak porowatość. Użycie mieszanki Ar/CO2 wzmacnia kontrolę nad procesem spawania, co sprzyja osiąganiu lepszej jakości spoin.
Jaki gaz jest najczęściej stosowany do spawania stali czarnej?
Najbardziej popularnym gazem wykorzystywanym w spawaniu stali czarnej jest dwutlenek węgla (CO2). Dzięki niskim kosztom i wysokiej efektywności, zapewnia on dobre wtopienie, co jest kluczowe dla uzyskania trwałych połączeń spawanych. Niemniej jednak, stosowanie CO2 może skutkować większą ilością rozprysków, co bywa uciążliwe. Mimo to, zalety tego gazu często przeważają nad jego wadami.
Aby zwiększyć jakość spoin, coraz częściej używa się mieszankach gazów, zazwyczaj z dominującą ilością argonu i dwutlenku węgla. Takie połączenie łączy pozytywne właściwości obu gazów, co skutkuje stabilnością łuku spawalniczego i redukcją niepożądanych zjawisk, takich jak rozpryski.
Decyzja dotycząca wyboru gazu powinna być ściśle powiązana z wymaganiami konkretnego projektu oraz wykorzystaną techniką spawania, co przyczynia się do osiągnięcia najlepszych wyników. W przypadku stali czarnej, odpowiednie gazy osłonowe są fundamentem jakości spoin oraz efektywności całego procesu spawalniczego.
Jak dobiera się gaz do spawanego materiału przy użyciu metody MIG/MAG?
Wybór gazu osłonowego w metodzie MIG/MAG ma fundamentalne znaczenie dla uzyskania wysokiej jakości spoin. Kluczowymi czynnikami przy decyzji są:
- rodzaj materiału,
- jego grubość,
- specyfikacja projektu.
Odpowiedni gaz wpływa na skuteczność spawania oraz na trwałość połączeń. Dla stali węglowej najczęściej stosuje się:
- dwutlenek węgla (CO2),
- mieszankę argon-dwutlenek węgla (Ar/CO2).
CO2 jest relatywnie tani i zapewnia doskonałą penetrację, ale może generować większą ilość odprysków. Alternatywnie, mieszanka argonu z CO2 w proporcji 82% argonu i 18% CO2 pomaga stabilizować łuk spawalniczy, co z kolei minimalizuje rozpryski, poprawiając tym samym jakość spoiny. Jeśli chodzi o stal nierdzewną, rekomendowane są:
- gazy obojętne, takie jak argon,
- często z dodatkiem niewielkiej ilości CO2 lub tlenu.
Dla aluminium, najlepiej sprawdzają się:
- argon,
- mieszanki z helem, które pozwalają na odpowiednie wtopienie i estetyczny wygląd spoin.
Warto zwrócić uwagę na normy, na przykład DIN EN 439, które pomagają w klasyfikacji gazów oraz ich doborze do konkretnych zastosowań. Kluczowe jest zrozumienie, jak właściwości gazów, takie jak stabilność łuku, wpływają na jakość spoiny, co jest niezbędne do osiągnięcia najlepszych rezultatów w spawaniu metodą MIG/MAG.
Jak gazy osłonowe chronią materiał spawany przed szkodliwymi reakcjami?
Gazy osłonowe odgrywają fundamentalną rolę w zabezpieczaniu spoin przed szkodliwymi reakcjami chemicznymi w trakcie spawania. Tworzą one barierę pomiędzy stopionym metalem a otaczającą atmosferą, co skutecznie zapobiega:
- utlenianiu,
- azotowaniu,
- innym niekorzystnym procesom,
które mogą osłabić połączenie. Wykorzystanie gazów obojętnych, takich jak argon czy hel, znacząco minimalizuje ryzyko wystąpienia porowatości. Argon, jako gaz nie reagujący z metalem, zapewnia czystość i brak zanieczyszczeń w procesie spawania. Natomiast gazy aktywne, takie jak dwutlenek węgla (CO2), potrafią wchodzić w interakcje z metalem. Tego typu kontrolowane reakcje mają wpływ nie tylko na właściwości spoiny, ale także na jej głębokość penetracji.
W przypadku spawania stali czarnej, dwutlenek węgla bywa preferowany głównie ze względu na swoją przystępną cenę i efektywność, gdyż zwiększa głębokość wtopienia, aczkolwiek stwarza większe ryzyko rozprysków. Mieszanka argonu z CO2 łączy zalety obu gazów, co przyczynia się do poprawy jakości spoiny oraz stabilności łuku spawalniczego. Właściwy wybór gazu, dostosowany do konkretnego materiału i metody spawania, jest kluczowy dla zapewnienia wysokiej jakości połączeń. Dobrze dobrany gaz nie tylko przyczynia się do lepszych wyników w spawaniu, ale również zwiększa trwałość wykonanych spoin.
Jakie czynniki wpływają na jakość spoiny podczas spawania stali czarnej?
Jakość spoiny podczas spawania stali czarnej uzależniona jest od wielu istotnych czynników. Wśród nich kluczową rolę odgrywa wybór gazu osłonowego.
- dwutlenek węgla (CO2),
- mieszanka argonu z CO2 (Ar/CO2).
Choć CO2 sprzyja głębszemu wtopieniu, wiąże się z większym ryzykiem powstawania rozprysków. Z kolei mieszanka argonu z CO2, dzięki swojej stabilności, minimalizuje te problemy, co przekłada się na poprawę jakości spoin. Oprócz tego, nie bez znaczenia są także parametry spawania, takie jak:
- prąd,
- napięcie,
- prędkość.
Odpowiednie ustawienia tych wartości są kluczowe, aby otrzymać trwałe i estetyczne spoiny. Czystość materiału również wpływa na końcowy efekt; zanieczyszczenia mogą prowadzić do pojawiania się wad, takich jak porowatość czy utlenienie. Technika spawania oraz umiejętności spawacza mają istotny wpływ na finalny rezultat. Doświadczeni spawacze potrafią dostosować proces do specyficznych warunków projektowych, co znacząco podnosi jakość wykonania.
Nie można również zlekceważyć znaczenia sprzętu spawalniczego. Nowoczesne urządzenia, takie jak spawarki MIG/MAG, mogą znacznie poprawić efekty pracy. Warto zatem zauważyć, że jakości spoiny przy spawaniu stali czarnej to złożony temat, w którym istotne są zarówno dobierane materiały, jak i zastosowane techniki spawania oraz doświadczenie spawacza. Staranność w doborze parametrów oraz dbałość o szczegóły są kluczowe do osiągnięcia spoin trwałych, estetycznych i wolnych od defektów.
Jakie błędy należy unikać podczas wyboru gazu do spawania?
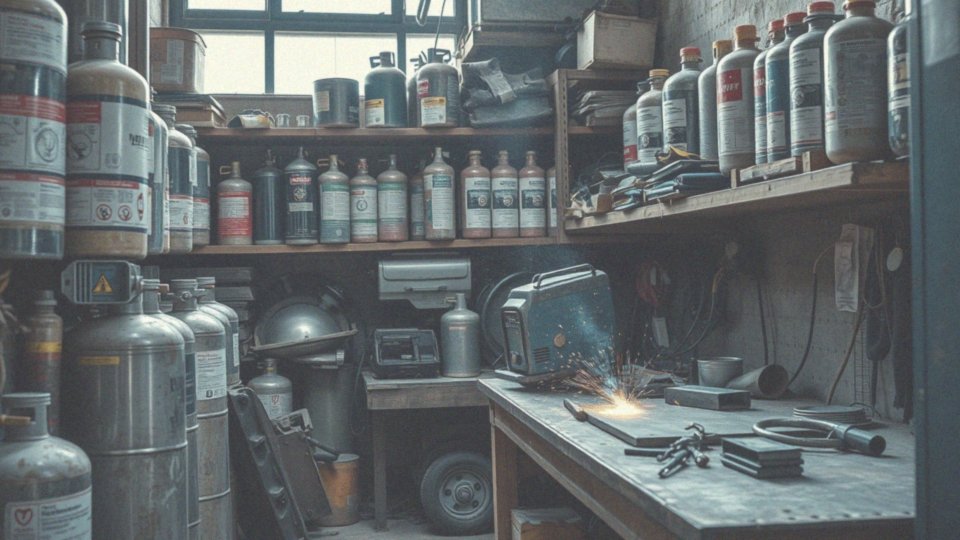
Wybierając gaz do spawania, należy unikać powszechnych błędów, które mogą negatywnie wpłynąć na jakość wykonywanych spoin oraz ogólną wydajność całego procesu. Oto najważniejsze potknięcia, na które warto zwrócić uwagę:
- Niewłaściwy gaz: Różne materiały wymagają odpowiednich gazów osłonowych. Przykładowo, stosowanie dwutlenku węgla (CO2) przy spawaniu aluminium może pogarszać jakość spoiny, ponieważ gaz ten reaguje z metalem, co prowadzi do niepożądanych efektów.
- Zanieczyszczony gaz: Użycie gazu, który jest zanieczyszczony, może skutkować wadami spoin, takimi jak porowatość czy utlenienie. Niezwykle istotne jest, aby gaz był czysty i pozbawiony jakichkolwiek zanieczyszczeń.
- Nieodpowiedni przepływ gazu: Zbyt niski przepływ nie zapewni dostatecznej ochrony spoiny, natomiast zbyt wysoki może zwiększać ryzyko powstawania rozprysków. Dlatego właściwe ustawienie parametru przepływu jest kluczowe dla stabilności łuku spawalniczego.
- Lekceważenie zaleceń producenta: Zrozumienie wytycznych dotyczących doboru gazu i jego ustawień zdecydowanie może poprawić efektywność spawania. Zawsze warto sięgnąć po dokumentację techniczną sprzętu, aby uzyskać najlepsze wyniki.
- Niedostosowanie do warunków: Czynniki takie jak wiatr, temperatura czy wilgotność mają istotny wpływ na działanie gazów osłonowych. Ignorowanie tych elementów może prowadzić do obniżenia jakości spoiny.
Unikanie tych błędów jest kluczowe dla uzyskania wysokiej jakości spoin oraz zwiększenia wydajności spawania. Odpowiedni dobór gazu, dostosowany do specyfiki materiału i metody spawania, odgrywa zasadniczą rolę w osiągnięciu sukcesu w tym procesie.